Distribution center assessment, design and implementation
Distribution centers, fulfilment centers and warehouses are a critical part of any supply chain. Labor shortages and increased labor costs are changing the return of investment of automation. Various levels of automation are emerging.
The availability of real estate can be tight. Inventory levels are dropping reducing the capacity needs for storage. All these factors force companies to re-think their distribution center Our team of experts can support you with the right fit distribution center from a labor, space and equipment perspective. Together with our strategic partner St.Onge Company, we assess, (re)design and implement distribution centers - current or new (greenfield). We focus on capabilities, capacities, processes, lay-outs, IT, and technology. Ensuring that your distribution footprint is optimized for the requirements of your supply chain.
The function of distribution centers has developed from a simple place to store your products to a competitive advantage. Nowadays, different sales channels like distributor, wholesale, retail, and ecommerce each have their own requirement which your distribution center has to fulfill. The optimal distribution center balances the three main resources labor, space and equipment depending on the need for flexibility, product characteristics, and order profile. Investments in for example automation and mechanization (equipment) can reduce the need for labor and space.
Assessing your distribution center on time brings savings or cost avoidance by extending the lifespan of current buildings or applying new concepts to reduce building and labor costs dramatically. In today’s technology landscape including application of robotics and the scarcity of labor in some markets to staff DCs, finding the right balance between occupancy, investments in equipment and labor is key.
E-commerce is gaining importance and has a great influence on your distribution center. Increased levels of ecommerce mean that instead of pallet or master carton, your warehouse operations now have to support increasing levels of single item picking processes. This impacts the workload and combined with labor scarcity can be a strong motivator for automation. Based on a BCI’s distribution center audit and assessment – taking into account amongst others ecommerce growth and labor scarcity – we can create a distribution center road map to help you make an informed decision on your next step: optimize the current location, or move to a new facility.
Distribution Center Audit & Capacity Assessment
The distribution center audit & capacity assessment combines the available capability and capacity and evaluates whether this will enable the distribution center to support current and future developments. Important elements are the existing storage & MHE technology, availability of labor, forecasted growth in demand and number items (SKUs), sales channels and picking profiles, required flexibility to accommodate seasonality (average-to-peak ratio). This typically is important to distribution centers that are inefficient or operating beyond targeted capacity, utilize off-site overflow locations, or are reaching the end of the contract. The distribution center audit and assessment is important for both your own owned & operated distribution centers as well as to evaluate your outsourced distribution footprint.
We use our proven 3-step approach to audit and assess distribution centers:
Step 1: Access current situation
Step 2: Identify and quantify opportunities for improvement
Step 3: Create roadmap for a) immediate action, b) short-term initiatives, c) mid-term initiatives
Labor analytics
Many distribution centers rely on human talent to operate. Given the volatility in demand and shortage of labor in distribution centers, it is key to locate distribution centers in the right location to have access to a proper labor pool. When located, key is to recruit and retain the right talent to operate the distribution centers. BCI can advise customers from a labor analytics perspective, benchmark labor costs and provide tactics to attract and improve retention rate of staff using BCI’s proprietary IDEAL approach (In-DEpth Assessment of Labor markets).
Distribution / Facility Center Design
During this phase we develop together with you a financially viable and optimal lay-out, accounting for the required material handling and warehouse management systems, taking into account your supply chain profile and objectives. The initial design phase generates the (financially) business case to onboard (senior) management and includes the optimized solution with a feasible layout design, the right material handling equipment and WMS functionality. We assess a full range of alternative solutions ranging from conventional to fully automated systems and robots. The base case design is a manual design compared and evaluated with various automated material handling equipment solutions.
We use our proven 4- step approach to design distribution centers:
Step 1: Determine the location from a real estate and labor perspective
Step 2: Identify requirements and processes of distribution center
Step 3: Translate requirements in required material handling equipment and storage technology and automation
Step 4: Integrate requirements and create high level distribution center design
Procurement
After (senior) management approves the (re-) designed distribution center, we develop the functional systems design documentation and information systems specifications. You need these documents to reach out to the market and to be able to compare quotes (apple-to-apples). We can support you in this supplier selection process and help you with the evaluation, negotiation and contracting where applicable.
We use a proven 3-step approach for procurement of the (re-)designed distribution center:
Step 1: Determine building requirements, including sprinkler, IT, temperature control, BREAAM, security to name a few. This results in a “Schedule of Requirements” (SoR)
Step 2: Supplier selection process, based on step-1 documents to ensure apple-to-apples comparison
Step 3: Supplier evaluation and awarding, with Negotiation, and contracting of procurement
Implementation management
The most important step is implementation. Professional project management is key for a successful implementation. BCI has project and program management experts with extensive experience in developing, implementation, consolidation, opening and closing of Distribution center.
BCI is part involved in the implementation of 50% of BCI’s recommendations.
Technology: Mechanized/automated storage and advanced Material Handling Equipment (MHE)
Pick-to-light, Voice-picking, Pick stations, Goods-to-man, Man-to-goods, Conveyers, (Bombay) sorters, Automated Storage & Retrieval System (AS/RS), Miniloads, Shuttle, Vertical Carousels, Pallet racking (double deep, flow racks) Autostore, Reach truck, Forklift truck, Very Narrow Aisle truck (VNA), Automated Guided Vehicles (AGV), Cobots, Swarmbots, these are just a few of the available technologies. The amount technology options can be overwhelming. BCI helps you to navigate this world and provide guidance on what makes sense for your operation and business.
We use our proven 5-step approach to identify the right level of automation for your organization:
Step 1: Access current situation
Step 2: Benchmark current performance and used technology/automation with industry peers
Step 3: Identify relevant technology/automation
Step 4: Create business case to support decision making process
Step 5: Recommendation and roadmap to implementation
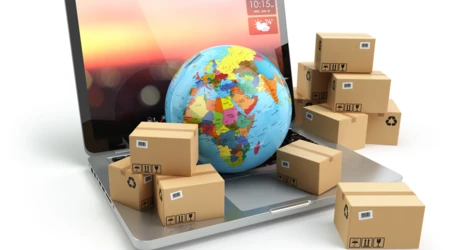
16 February 2022