Supply Chain
Within all production, wholesale and logistics companies, the set-up and organization of the supply chain is vital. BCI Global translates your business strategy in a feasible supply chain strategy. BCI’s service offering includes all aspects to develop and properly implement the right supply chain strategy through solid research and a feasible operating model. Our focus, as a supply chain consultant, is delivering results.
Being able to contribute to the further expansion of BCI Global in my new role as partner is a great challenge. This firm has an excellent reputation
We are here to dive into the world of partners in the business environment. With a CMO, with a packaging company, with your logistics provider. The question here is: what is real partnership, what is the essence of true partnerships, and why do we seek business partners?
Road and parcel transport costs on the rise again with gross rate increase expectations of 4-7% for road and 5% for parcel next year. Ocean freight and air freight remain very volatile, according to BCI Global’s Transport Monitor
We believe that supply chain strategy should follow business strategy, based on clear customer requirements. Once defined, it drives the other functional strategies such as procurement, manufacturing, planning and distribution so that these are all aligned. The visual below highlights the dependency between the business strategy and the supply chain and functional strategies.
Key elements driving the business strategy include the overall vision, the geographical markets, the go-to-market strategy with clear service level requirements per product-market-channel combination. As companies are serving various customers with different products with varying characteristics, it is paramount to differentiate your supply chain per product-market-channel rather than having a single size fits all approach.
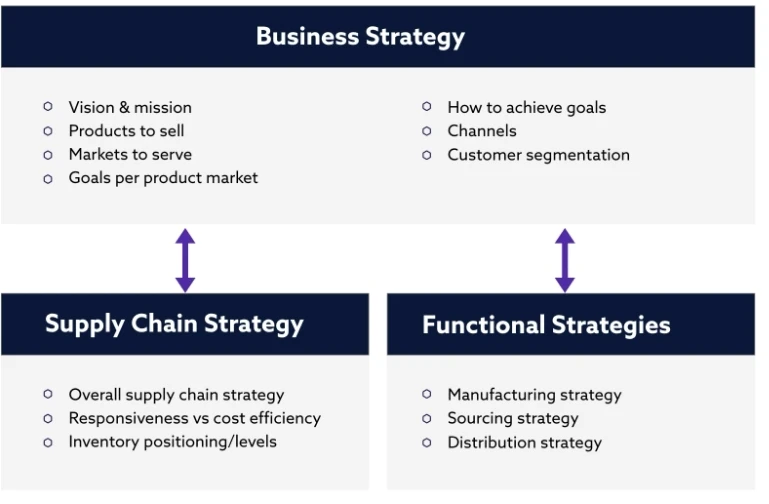
- Efficient
- Fast
- Continuous replenishment
- Agile
- LeanAgile
- Flexible
The table below provides more detail on these six archetypes.
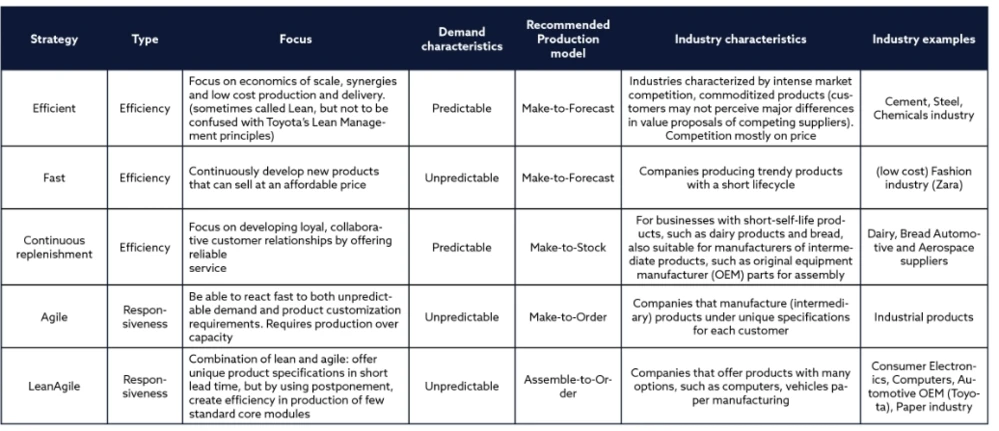
These archetypes fully describe all the supply chain process elements that are required to have a well-defined strategy. The BCI framework consists of 40 elements such as management focus, product related strategies (such as inventory strategy, level of customization), sourcing, production and fulfillment strategy elements. The benefit of using an archetype, is that all functional elements are internally consistent and aligned with each other.
Your company can use the archetype that fits best to design your supply chain strategy. This is done through a 3-step approach:
- Identify key characteristics of your business environment, customer requirements and the unique value proposal you are offering to the market.
- Based on this, the framework will indicate which archetype supply chain strategy has the best fit. You can use this as the foundation to design your own supply chain strategy.
- Once the overall supply chain strategy is determined, the framework will then give guidance on the configuration of your supply chain processes at functional level below (through these 40 elements). Of course you could deviate from this guidance, and in some cases that might be justified on some uniqueness in your business, but in most cases following the framework guidance yields the best results. In this way the BCI framework shows how overall supply chain strategy sets the direction for each function, to ensure alignment between each functional strategy and the overall supply chain strategy.
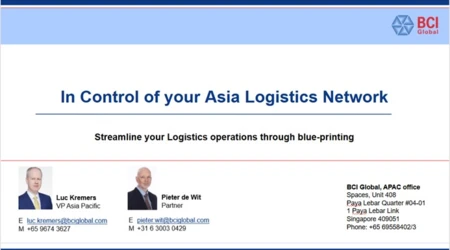
01 May 2025

01 May 2025
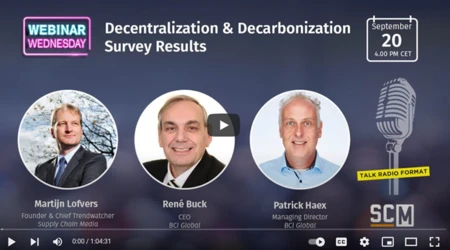
20 September 2024
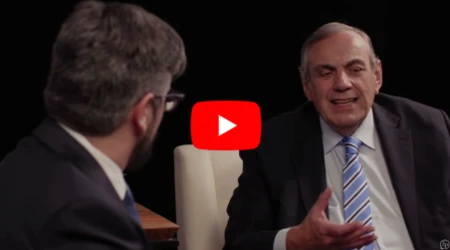
23 April 2024
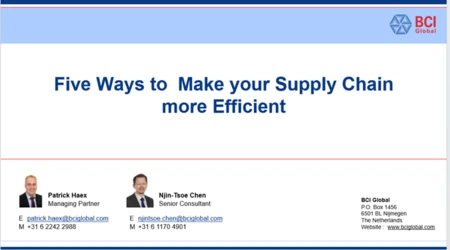
22 April 2024
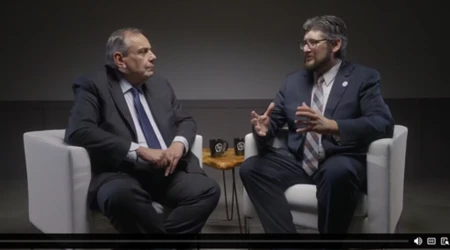
12 September 2023
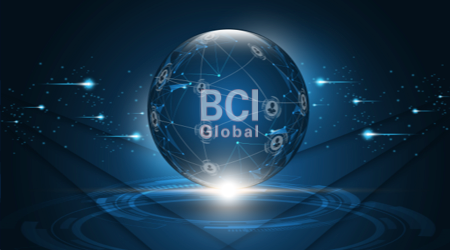
15 January 2025
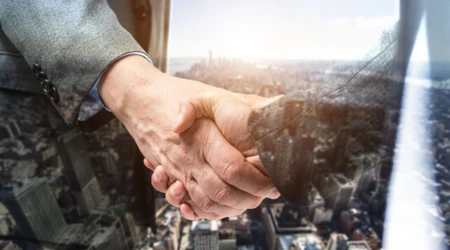
11 December 2024
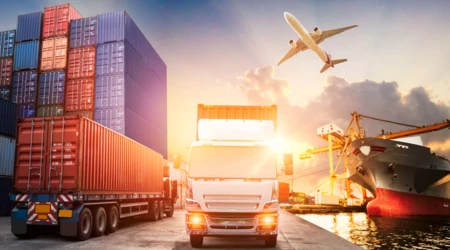
05 December 2024